7 sustainability takeaways from packaging sorting and recycling plants
Sustainability
January 10, 2018Reading time: 4 minutes
Sustainability experts at Amcor outline lessons learnt during visits to packaging sorting and recycling facilities in the U.S. and Germany.
Sustainability experts at Amcor outline lessons learnt during visits to packaging sorting and recycling facilities in the U.S. and Germany.
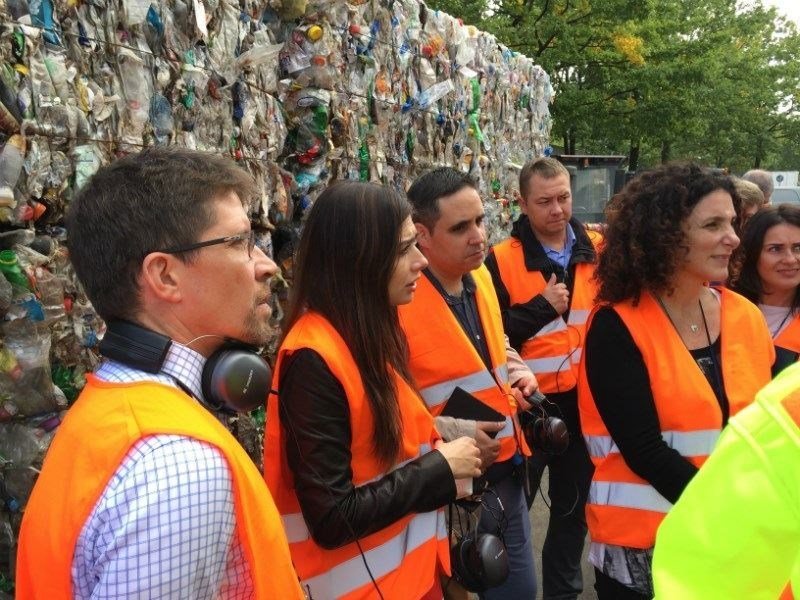
The very thing that makes flexibles the perfect packaging for everything from nuts to steak – thin layers that create optimum protection for the product inside – has traditionally made it harder to recycle. Historically, high-barrier flexible packaging hasn’t been collected for recycling in most countries (with Germany a notable exception), but this is now changing.
We’re researching new ways of making flexible packaging easier to recycle, as well as collaborating with like-minded companies to enable flexible packaging to be accepted for recycling in the first place – and learning from sustainability experts in sorting and recycling plants around the world. Here’s what we learnt during recent site visits, led by Amcor’s Gerald Rebitzer in Europe and Fabio Peyer in North America.
1. FLEXIBLE PACKAGING CAN BE SORTED INTO RECYCLING STREAMS
In Germany and some other European countries, flexible packaging is already sorted from other types of household packaging by consumers into specific collection bins or bags. It is then further separated based on material composition at sorting facilities. Here the challenge is making that sorting more precise and efficient.
In North America, the most common recycling system is single stream, meaning all recyclables, including glass, metal and paper, is collected together. And the collection of flexible packaging for recycling is still very limited. Tests conducted as part of the Material Recovery for the Future (MRFF) project showed us that adding flexibles to the single-stream collection system is technically viable, provided the appropriate sorting equipment is installed at sorting facilities. These results are a promising first step toward a future where consumers across the US and Canada would have the opportunity to put flexible packaging in their recycling bins.
2. GERMANY’S ‘YELLOW BAG’ AND ‘GREEN DOT’ SYSTEMS ARE WORKING WELL
In Germany, the government asks people to put their used ‘light’ household packaging into yellow bags or bins (everything except glass and paper, which are collected separately). The yellow bags are then sent to dedicated sorting facilities. Brand owners cover the costs of collection and management of post-consumer packaging waste through a Green Dot fee on all their packaging, where the fee depends on the amount and type of packaging material used. At the same time, Germany has banned plastics from their landfills. Today, virtually no plastic is landfilled in Germany, and recovery rates are among the highest in the world.
3. ADVANCED MATERIAL RECOVERY FACILITIES SORT HUNDREDS OF TONNES PER DAY
The Lobbe Sorting Facility in Germany sorts 18 tonnes of packaging materials per hour. The yellow bags arrive in lorries and the packaging is taken through various sorting technologies. Sorting then identifies each pack’s material composition and separates different types of plastics, paper and metals into the appropriate recycling streams.
What makes flexible packaging more challenging to sort is that it can be made of mixed materials. Added to that, its material efficiency can also pose a challenge. Flexible packaging is lightweight and uses significantly less material than plastic bottles or aluminium cans, for example. Both factors require sorting technology to be more sensitive and precise. At Amcor, we’re learning how to make it easier to identify and sort bags, pouches, lidding and wrappers based on material composition.
4. WITH STATE-OF-THE-ART TECHNOLOGIES, MATERIALS AS SMALL AS 20MM CAN BE SORTED
The smallest piece of material sorted by the machines at the Lobbe facility is 20mm, compared to a minimum of 4cm at older facilities. The materials are then compacted into bales of anywhere between 250kg and 400kg, which are then sent to recyclers and recovery operations.
5. MAKING SURE CONTAMINATION LEVELS IN BALES ARE LOW IS KEY
It’s important that the bales are sorted efficiently enough to meet the specification required by the recycler. When recyclers buy bales from the Lobbe facility, they’ll test the quality. If it’s not high enough, they’ll be sent back, introducing extra transport, energy use and costs into the process. It’s therefore of utmost importance that flexible packaging doesn’t end up contaminating other value streams when added to the incoming feedstock for sorting.
6. NEAR-INFRARED TECHNOLOGY HAS HIGH POTENTIAL FOR SORTING FLEXIBLES FROM PAPER IN NORTH AMERICA
The two-dimensional format and shape of flexible packaging makes it behave like paper when running through sorting centers in North America, also known as material recovery facilities or simply MRFs. Before adding flexible packaging to the MRF system, additional sorting technology would be required to separate it from the paper stream. During our MRF visits in the U.S., we looked at phase two of the MRFF project (Material Recovery for the Future), which included testing technologies to separate flexible packaging from paper in a real-world setting. The tests conducted in actual MRFs showed that near-infrared sensors can separate plastic films from the paper stream at high speed and high yield. This technology is already used in much of Europe to address various sorting demands, and can be easily adapted to fit North American systems, making it a natural candidate for potential MRF upgrades.
7. VALUE CAN BE FOUND IN RECOVERED MATERIALS
In Germany, mixed materials that can’t be cleanly separated into recycling streams end up in a mixed plastics stream and are used as refuse derived fuel (RDF), a replacement for fossil fuel based fuels for energy production in cement mills. Only 6% of the whole input ends up as waste (‘residual’ stream) in incineration plants. While this avoids packaging ending up in landfills, our goal is to work with our partners to firstly reduce the amount of material in the mixed plastics and ‘residual’ stream, and secondly identify markets for these materials that would put them back into use.
Significantly increasing the share of flexible packaging that’s recycled is an objective of our collaboration with the Ellen MacArthur Foundation’s New Plastics Economy, as well as the CEFLEX initiative in Europe and MRFF initiative in North America. The second phase of the MRFF project also included a project dedicated to finding profitable recycling outlets for the materials recovered so that there’s an incentive for separating the materials. The third phase will be to identify a pilot community and recovery center to test collection of flexibles packaging and sorting using near-infrared technology over a longer period.
Flexibles offer a resource-efficient, low-cost, resilient and durable way to keep food and other packaged goods fresher and safer for longer. While they do pose some recycling challenges, we have the expertise to improve the process and be sustainability leaders by working with partners like the New Plastics Economy, MRFF and CEFLEX to make positive changes.
Contact Amcor to learn more about opportunities for recycling and recovery of flexible packaging in different countries.
Related Insights
5 things to know about the EU Packaging and Packaging Waste Regulation
March 16, 2023
Perhaps you’ve heard about the new European Union draft Packaging and Packaging Waste Regulation (PPWR). Maybe you even know a little about it. Yet, you might be wondering what it means for your business, your consumers, and the planet. Read on to learn more.
Perhaps you’ve heard about the new European Union draft Packaging and Packaging Waste Regulation (PPWR). Maybe you even know a little about it. Yet, you might be wondering what it means for your business, your consumers, and the planet. Read on to learn more.
Chemical recycling for flexible plastic packaging in Europe
February 15, 2023
What is chemical (or advanced) recycling? And what opportunities does this emerging process present for flexible packaging? We'll take a focused look at Europe.
What is chemical (or advanced) recycling? And what opportunities does this emerging process present for flexible packaging? We'll take a focused look at Europe.
Amcor’s 2025 pledge: important for all our stakeholders
January 23, 2018
The first global packaging company pledging to develop all its packaging to be recyclable or reusable by 2025, Amcor CEO Ron Delia says ambitious goals and collaboration can benefit all stakeholders.
The first global packaging company pledging to develop all its packaging to be recyclable or reusable by 2025, Amcor CEO Ron Delia says ambitious goals and collaboration can benefit all stakeholders.