Comparing 3 Popular Healthcare Packaging Formats: Form Fill Seal, Thermoforming, and Pouches
Medical
August 23, 2023Reading time: 3 minutes
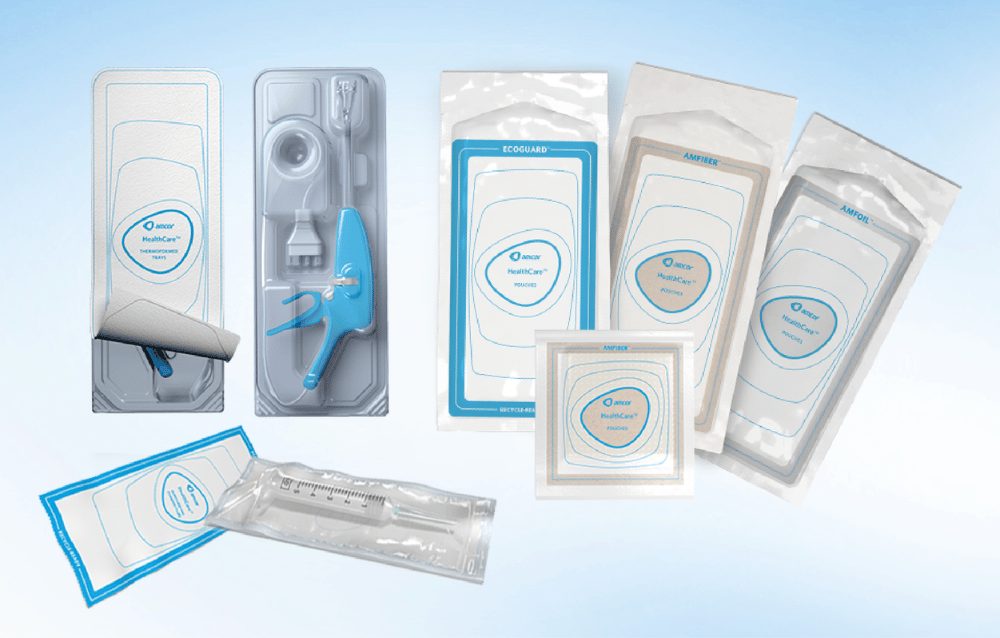
Healthcare packaging needs to be protective and proficient in maintaining product integrity and patient safety. There’s the obvious function of protecting medical devices and products from physical damage, but there are other medical packaging considerations — sterilization, regulatory compliance, productivity cost, ease of use, sustainability, etc.
Aligning medical packaging needs with the available options requires informed decision-making. Form fill seal packaging, thermoformed packaging, and pouches are all effective solutions; the right choice for a particular application often comes down to nuanced differences between these three popular packaging formats.
This quick-reference comparison provides guidance on healthcare packaging methods to help streamline the packaging selection process.
Form Fill Seal Packaging
Form Fill Seal (FFS) refers to producing sealed packages from a roll of flat, flexible film. The three steps listed in the name are accounted for in one fully automated process that takes place on special FFS equipment:
-
Form: Film is fed into a FFS machine and formed into a bottom tube-like enclosure large enough in depth, width, and length to accommodate the specific medical device. This is the foundation of the package
-
Fill: The formed films are filled with the medical device via automated product placement
-
Seal: The FFS machine feeds a top film or breathable layer on the formed enclosure and creates seals along the package top edges, effectively covering and sealing the medical device
Medical device manufacturers have the flexibility of choosing FFS materials that fit their specific objectives depending on the device being packaged and application requirements. FFS films are made from a wide breadth of plastic materials that cater to performance requirements such as abrasion protection, puncture resistance, clarity, and sustainability in addition to costing and automation productivity considerations.
FFS films can be lower cost compared to other packaging formats but they require expensive specialized automated equipment to process. That is why FFS films are generally applicable for high volume device packaging production and automation. Those high volumes and related automation savings would justify the substantial investment in equipment.
Thermoformed Tray Packaging
The thermoforming process for healthcare packaging introduces pliable plastic into a mold to obtain a package shape that corresponds with the medical device. Trays are designed with cavities and compartments that snugly fit a medical device and any components. A lid is used over the tray to seal and cover the contents.
Thermoformed medical packaging is a widely used solution because of its protective qualities, which is especially important for high-value or delicate medical devices and instrumentation. Since thermoformed trays are shaped to the specific characteristics of a device or product, they also aid in:
- Prohibiting accidental device activation
- Supplying the rigidity necessary to ensure precise handling and presentation
- Ensuring devices remain in place and sterile barriers remain intact
- Right-sizing packaging to minimize waste and promote more sustainable solutions
- Contamination-free, controlled openings at the point of use by incorporating easy-to-use peel systems
Thermoforming materials are as versatile as the packaging. A full range of material options are available for trays (HDPE, PP, PETG, HIPS, APET) and lidding (breathable materials, foils, some polymers) which support design innovation and the overall thermoforming process.
Thermoformed packaging is generally more expensive than other packaging formats such as FFS films. However, this cost is outweighed by the benefits noted above.
Pouch Packaging
Pouch medical packaging brings together two webs of engineered materials that are heat-sealed on three sides to form a flexible enclosure that can be produced in a wide range of shapes and sizes.
Pouches generally fall in one of three medical packaging categories:
- Breathable pouches withstand Ethylene Oxide (EO) sterilization applications. The porous web provides sterility and breathability, as well as adaptability to pressure or altitude changes
- Film-to-film pouches are solutions that align best with gamma radiation and electronic beam sterilization, and provide enhanced product protection. Extrusion film materials can be gauged to accommodate device weight, puncture resistance, and end user requirements such as visibility and peelability
- High barrier pouches prohibit light, oxygen, and moisture from penetrating packages and causing device degradation. High barrier pouches are particularly effective in maintaining the integrity of cardiac catheters, guidewires, implants, diagnostics, and drug-coated products among other applications
Pouches are a key solution for medical device sterilization, protection, and safety. Each design takes specific device characteristics and application environments into consideration.
Pouches are generally more expensive than other packaging formats such as FFS films yet lower cost compared to thermoformed trays. Pouches are ideal for medical devices that do not need the benefits of thermoformed trays and have low to medium production volumes that cannot justify investing in FFS automated equipment recruitment; instead, use manual or semi-automated production processes.
The Next Step in Informed Decision-Making
The comparisons briefly outlined in this article are meant to bring medical device manufacturers and decision-makers up to speed on potential healthcare packaging solutions. Knowledge is power, and maybe it’s time to take the practical next step.
Reaching out to an experienced medical packaging partner such as Amcor bridges information and solutions, as does the insights you’ll find in The Insider’s Guide to Sterile Barrier Packaging.
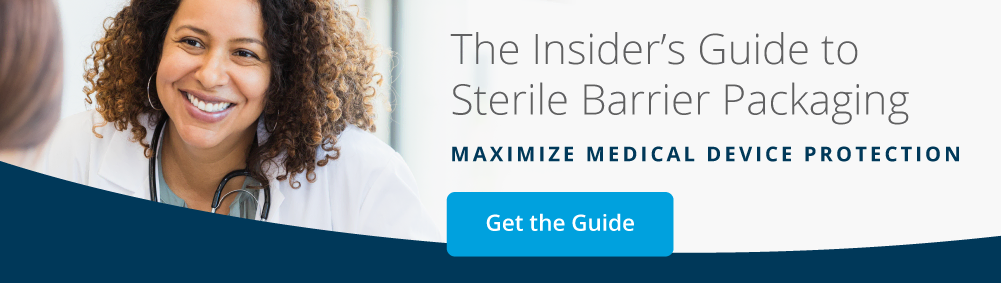