Checklist: Medical Device Packaging Best Practices for New Product Launches
Medical
May 3, 2023Reading time: 3 minutes
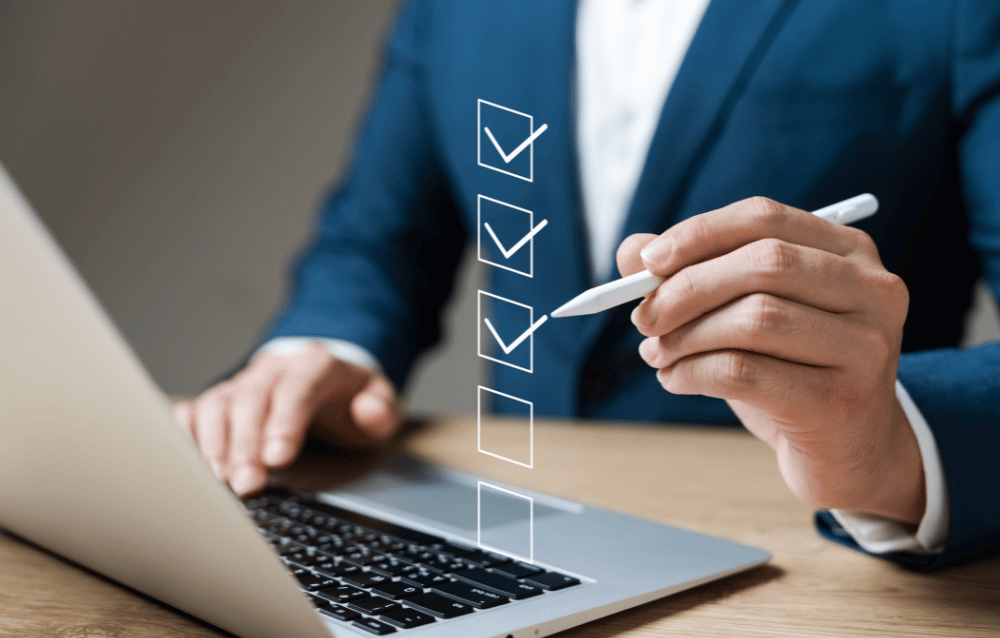
Introducing a new medical device is an exciting and often stressful time for manufacturers. The time and cost of new product development are typically significant investments, let alone managing the risk of getting the devices to market safely.
Medical device packaging is essential for patient safety because it protects products from damage and contamination. Its function is so integral to successful product launches that packaging should be developed in tandem with the device to ensure proper performance.
Collaborating with an experienced medical packaging supplier in the earliest medical device design stages and throughout new product development is the key to risk mitigation. Their guidance in implementing medical device packaging best practices aligns packaging with the application’s needs and overall operational goals.
Checking in on medical device packaging considerations
A glance at the following checklist of medical device packaging requirements and recommendations confirms the need for assistance from a packaging partner. Each focus section raises questions that need definitive answers in order to match packaging to the new medical device.
Best Practice Focus: Regulatory compliance
Medical device packaging requirements are highly regulated by the U.S. Food and Drug Administration (FDA). The best medical packaging suppliers will provide data to support the 11607 compliance data, and be certified to the ISO 13485 quality standard required for medical device companies. The overall project compliance could be compromised if packaging lags behind the product development process.
The input of medical packaging experts throughout product development is critical to understanding:
- Are there potential packaging design or manufacturing problems that could cause delays?
- Is the package optimized for the device?
- Are additional package features required?
- Is the required 11607 data complete?
- Are patient health and safety definitively protected?
Best Practice Focus: Product protection
During medical device development, engineers commonly draw on their experience with certain packaging materials and formats to determine possible solutions.
Although primary focus is always on sterilization efficacy and product protection, the entire system needs to be examined for vulnerabilities:
- Will the proposed material combination handle the worst case product configuration in ship testing AND in sterilization?
- Are there any potential interactions between packaging or print and sterilization methods?
- If defects are encountered in aggressive ship testing, your packaging partner should be able to assist in identifying failure mode and recommending materials to eliminate defects. Beginning the development process together allows for iterative testing if needed
Best Practice Focus: Package testing
Validating medical device packaging is a collaborative effort between manufacturers and packaging suppliers. During testing, parameters are intentionally challenged on the manufacturing process, sterilization, and thorough distribution testing to verify:
- Did the packaging perform as intended and anticipated?
- Did the device remain fully protected and sterile?
- Was there any interactions noted between the medical device and the packaging?
- Is gathered data sufficient for submission to regulatory agencies to establish compliance?
Amcor provides an additional measure of package testing through prototyping. Knowing with certainty the design is validated with physical testing for performance, safety, and format provides confidence in taking the solution to production.
Best Practice Focus: End user experience
Packaging must remain free of contamination, materials failure, or seal failures to ensure medical devices are delivered to healthcare facilities ready to use. Once at the facility, however, packaging must also perform to end user expectations:
- Is the medical device visible and properly oriented?
- Can the package be easily opened by staff and presented to doctors or surgeons?
- Does the package label contain all necessary information?
- Are the packaging materials and characteristics adequate for protecting medical devices from moisture, oxygen, and light egress if stored for an extended period of time?
Best Practice Focus: Supply chain management
Business continuity is a hot-button topic, especially in the medical industry. Like many others, medical packaging supply chains proved vulnerable to disruption during the pandemic, causing manufacturers to rethink their supply chain strategies.
Materials, labor, and transportation must be consistently available and unified to manage supply chain risk. Further, the suppliers chosen must be more than experienced in medical packaging; they need to demonstrate capabilities that promote business continuity. Does the packaging supplier have:
- Reliable sourcing through global reach?
- Validated alternate materials and processes?
- An established supply chain risk-mitigation and management plan?
- Action-oriented, responsive communication and service?
There’s a lot to consider when taking a new product to market. Packaging best practices should be a top priority because they do more than guide medical device protection — they help keep patients safe.
Working with a world class packaging supplier such as Amcor in the earliest stages of new product development ensures packaging characteristics align with product needs, including best materials, sterilization methods, and more. Explore the possibilities in The Insider’s Guide to Sterile Barrier Packaging.
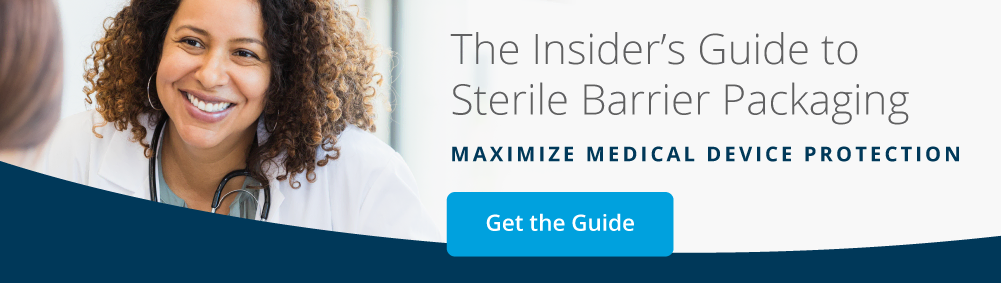