Comparing Common Form Fill Seal Materials for Healthcare Packaging
Medical
April 22, 2025Reading time: 4 minutes
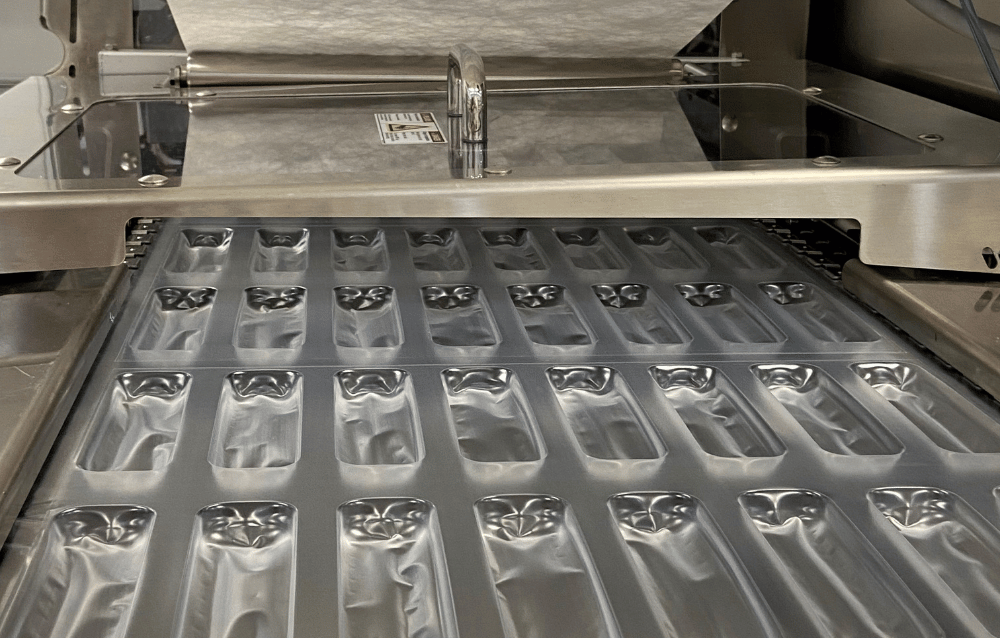
Form fill seal (FFS) packaging is a popular choice for healthcare. Because the FFS process allows the package to be formed, filled with product, and sealed in a single continuous, automated process, it’s often a cost-effective, efficient choice for packaging healthcare products.
Material selection is a critical part of FFS packaging production. Healthcare packaging needs to perform optimally and cost-effectively to protect, preserve, and present the product. Its performance depends on choosing the correct materials that balance key characteristics including strength, flexibility, formability, heat resistance, barrier protection, chemical resistance, and numerous other important properties.
Nylon, polyethylene (PE), and ionomers are three common resins used in FFS films. Each has its specific strength, and can be included in FFS films depending on the specific packaging design’s objectives.
Here, we’ll take a closer look at each material’s advantages and some of the most important factors to consider when choosing materials for healthcare packaging applications.
Key Characteristics to Consider in Healthcare Packaging Material
It would be a mistake to suggest there’s simply one “best” packaging material. Among nylon, PE, and ionomer resins, each presents important advantages that the others may not excel in. Normally more than one material type is needed to meet all the specified product and performance requirements, and materials are combined through the coextrusion process. Typical packaging requirements can include any or all of the following:
- Formability — draw down easily to create a well-defined package with consistent thicknesses and unblemished appearance with a wide processing window
- Sealability — a strong, sterile barrier seal, essential to maintain product integrity
- Flexibility and durability — mechanical properties robust enough to withstand transport and handling while maintaining sterility
- Biocompatibility — absence of adverse interactions with the human body (if intended for medical use)
- Regulatory compliance — meets requirements for safety and efficacy
- Printability — compatibility with packaging print methods and materials
- Barrier properties — protection from moisture, oxygen, and/or light
- Chemical resistance — capability to withstand exposure to the product without a reaction
Nylon: Tough Yet Temperamental
Nylon (polyamide) is a versatile polymer well-suited for high-performance FFS packaging and commonly used in protective healthcare packaging. It has excellent mechanical properties that include tensile strength,abrasion resistance, formability, flexibility, and resistance to heat, wear, and many chemicals. It is this combination of strength and abrasion resistance where coextruded structures containing nylon excel. Correctly designed, coextruded nylon films are normally the most likely FFS films to pass the rigors of ship testing at the thinnest gauge, especially when packaging sharp or heavy products.
Though most FFS applications often do not require barrier properties, if needed nylon provides a good barrier against oxygen and other gases. It’s not the best moisture barrier and if that is requred, it can be a component layer in a multi-material packaging solution with other higher barrier materials.
When extruded using Amcor’s proprietary ICE® process, nylon films have a clear, glossy appearance that allows for designs that present well. The downside can be higher FFS forming temperatures required with nylon films when compared to PE or ionomer. Also when exposed to certain chemicals, including isopropyl alcohol, nylon can deteriorate and become brittle over time.
Polyethylene: Jack-of-All-Trades
One of the most commonly used plastics in packaging, polyethylene (PE) films are durable and flexible for their price point. PE offers a practical FFS option that balances cost, formability, and relatively moderate strength. These practical considerations make it a popular choice for some healthcare packaging applications, especially those with a shallow draw.
PE is available in a variety of densities and categories, but it is the metallocene PEs that have made their mark in FFS packaging. These resins have excellent puncture strength and flex crack resistance, and also offer excellent recyclability. Since the abrasion resistance is not as high as nylon, PE films are the logical choice when packaging lighter weight products without sharp edges to balance formability and cost. PE films provide the added benefit of being the most green option compared to nylon and ionomers.
In select applications where barrier properties are required, the PE films normally used in FFS only have moderate gas and moisture barriers. However, these can be combined with modifiers to deliver excellent barrier protection, as in the case of Amcor AmSky™ pharmaceutical FFS bottom webs.
Generally, PE is a versatile, easily recyclable, affordable choice for FFS applications with moderate strength requirements.
Ionomers: Premium Performance
Ionomers are unique thermoplastics that combine durability, top shelf forming properties, and visual appeal.
Used in FFS bottom webs in the medical industry for decades, ionomer coextruded films are ideal when forming properties are the highest priority. Normally coextruded with PEs, ionomer webs have the largest forming window. They are often called upon to produce reliable packaging when equipment has limited capabilities, is older, or requires very thick gauges. Excellent forming combined with moderate abrasion resistance, good puncture strength, and flexibility provides a package that will pass ship studies while maintaining sterile barrier. Package appearance is further enhanced by good film gloss and clarity.
FFS films coextruded with ionomers have barrier properties similar to PEs, and are not normally used in those applications requiring barrier properties.
Though ionomer resins carry a higher material price than PEs, they are often the choice when the strength, toughness, clarity, and consistent appearance of a well-formed FFS package is required for medical devices.
Each Polymer Can Excel When Selected for the Right Application
We have outlined where each FFS film type excels. Ionomer coextruded films offer a standout combination of forming performance, durability, and visual appeal (often at the highest cost). For maximum protection and shelf life, ionomer is often a top choice.
Nylon coextruded films excel at combining flexibility with abrasion resistance, which is especially helpful for heavy or sharp products. These are strong films and are often the go-to choice for passing ship studies and maintaining sterility throughout the distribution process.
PE shines as a lower cost material with a good combination of puncture strength, flex crack resistance, and formability. Applications with shallow draw depths for moderate to lightweight products, or areas where the highest levels of recyclability is required are good matched for PE coextruded films.
Material selection requires a close evaluation of product protection requirements, environment, sterilization methods, product lifecycle, and regulatory requirements. Coextrusions and multilayer films are designed to combine optimal advantages of each material.
Learn more about material innovations that are advancing healthcare packaging when you download our free Insider’s Guide to Sterile Barrier Packaging. Click below for your copy.
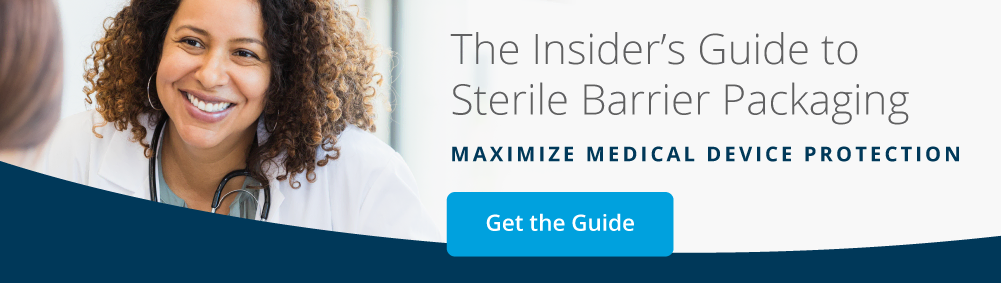